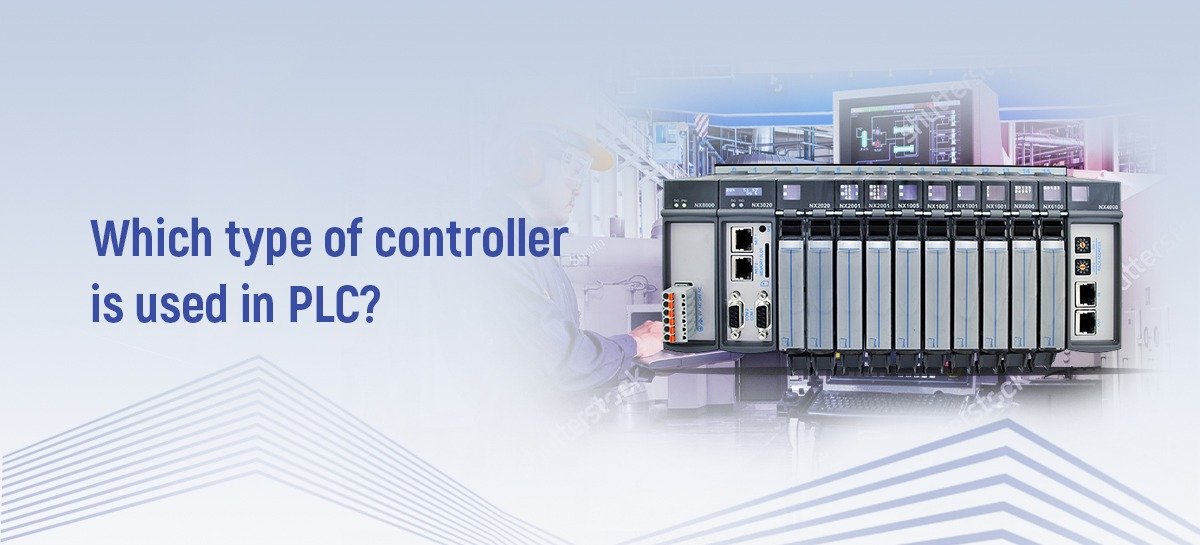
A Programmable Logic Controller (PLC) is an industrial device used to control and monitor various
operations within a particular system. It is a specialized computer that utilizes digital and analog input
and output modules to monitor and control the system.
PLCs typically use various types of controllers to control the system. On a high level, PLC controllers can
be categorized into three types:
- Input controllers: Input controllers are used to monitor the conditions of the system, such as
temperature, pressure, and voltage. - Output controllers: Output controllers provide control signals to the system, such as switching
an output device on or off. - Programmable logic controllers: Programmable logic controllers are used to program the logic
of the system, such as decision-making and looping, as well as monitoring and controlling the
system’s operation.
Types of Controllers Used in PLCs & Their Corresponding Uses
PLCs, or Programmable Logic Controllers, are used in various industrial automation projects and can be
controlled by either analog or digital systems. Let us look at some control systems that PLCs use.
- Analog control systems: These are used to control motor speed or valve flow and rely on
electrical signals (such as 4-20mA or 0-5V) to adjust the speed of a motor or the flow rate of a
valve. These control systems are often used for basic on/off control and basic positioning tasks. - Digital control systems: These are often used for more complex control applications. These
systems utilize more sophisticated algorithms to more accurately control the speed of a motor
or the flow rate of a valve. Digital systems typically use stepper motor controllers or servo motor
controllers, which are devices that use pulse-width modulation (PWM) to accurately control the
speed of a motor. - Motion control systems: These are more sophisticated digital control systems that are used to
control multiple motors simultaneously. These systems utilize sophisticated algorithms to
control multiple motors precisely and accurately, allowing for complex three-dimensional
movements and positioning. - Stepper motor controllers: These are used to send signals to stepper motors in order to control
the speed, position and torque of the motor. Stepper motors are typically used for applications
which require precise control and positioning, such as in robotic systems or materials handling
equipment. - Servo motor controllers: These are used to send signals to servo motors in order to control the
speed, position and torque of the motor. Servo motors are used for applications which require
precise control and positioning, such as in robotics and packaging machines.
How to Choose the Right Controller for Your PLC System?
There are a variety of controllers available for PLC systems, and choosing the right one for your
application can be a daunting task. It is important to consider a number of factors when selecting the
proper controller for your system, including size, speed, operating temperature, input/output port
types, and compatible hardware and software.
Size and Speed
The size and speed of a controller will largely depend on the size and complexity of your application. A
small controller can support simple applications with limited input/output capabilities, while larger and
faster controllers can support more complex applications with extensive input/output capabilities.
Additionally, some controllers are designed to handle multiple PLC systems simultaneously.
Operating Temperature
The operating temperature of the controller should be compatible with the environment in which it will
be used. In general, controllers should be able to operate in temperatures ranging from 0-60°C.
Input/Output Port Types
The type of input/output ports on the controller should match the type of input/output ports on the
hardware and software used by your system. Common input/output port types include USB, Ethernet,
and RS-232.
Compatible Hardware and Software
The controller should be compatible with the hardware and software used by your PLC system. Make
sure to check the specifications of the controller and the compatible hardware and software before
making a purchase.
By considering these factors, you can ensure you select the right controller for your PLC system. With
the right controller, you can maximize the performance and efficiency of your system.
Summing up
Messung’s highly efficient PLCs are popular in industrial settings across the world, such as factories,
waste-water treatment plants, and in the automotive industry. They are often used in applications
ranging from those that require precise control, such as controlling the manufacturing process in an
automated factory to temperature regulation a system, control the pressure of liquids, and to maintain
safety protocols.
Choose Messung today to achieve accurate and fast control in industrial processes. Make way for
efficient and effective automation of processes and reduce time and cost with Messung.