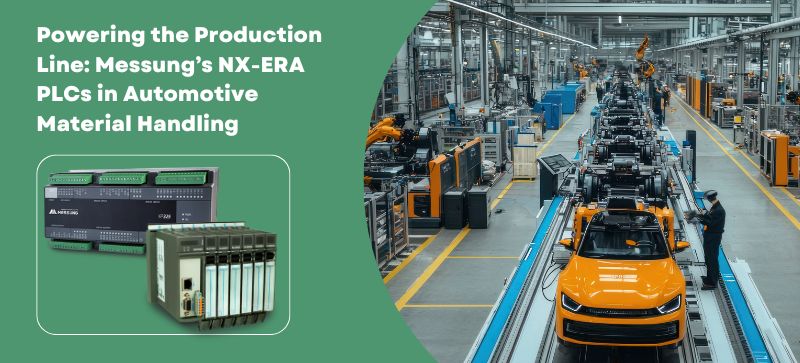
In automotive manufacturing, precision isn’t a luxury, it’s a necessity. From chassis and engine assembly lines to the press shop and paint line, seamless material handling is critical to keeping production on track. Whether it’s coordinating conveyors, pick-and-place systems, or synchronizing with robotic cells, the need for intelligent control is constant.
Messung’s NX-ERA PLCs deliver this control with unmatched flexibility. With native support for Modbus TCP/IP, Ethernet/IP, EtherCAT, OPC-UA, and IO-Link, they enable high-speed communication across robots, HMIs, VFDs, servo amplifiers, and central SCADA systems. Plus, with remote I/O modules and protocols like CANopen, our PLCs handle large-scale, distributed inputs and outputs effortlessly. Simply put, NX-ERA makes advanced, synchronized automation easy, even in the most demanding environments.
What is Material Handling in the Automotive Industry?
Material handling in the automotive industry involves the movement, positioning, storage, safety, and tracking of components and assemblies throughout the production process—from the arrival of raw materials to the final stages of vehicle assembly. Efficiency here is critical; any delay or misstep can disrupt the entire manufacturing flow.
Key areas such as the chassis and engine assembly lines, along with the press shop and paint line, rely heavily on sophisticated material handling systems, including conveyors, pick-and-place machines, and robotics, to keep production moving seamlessly. These systems must operate in perfect sync, often across large, distributed areas with thousands of I/O points.
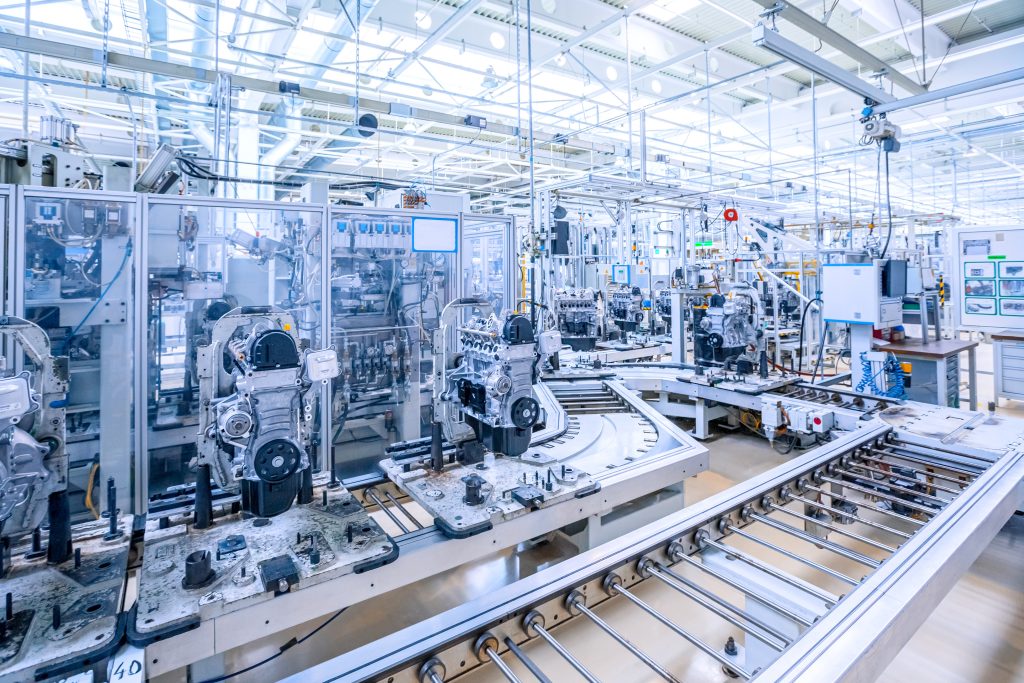
The Brain Behind the Brawn: NX-ERA PLCs
Our state-of-the-art NX-ERA PLCs including the NX-ERA Xpress and NX-ERA Jet, are compact PLCs designed for high-speed, reliable control. These programmable logic control systems are the heart of any automated material handling system. By offering real-time control, seamless connectivity, and robust communication protocols like Modbus TCP/IP, Ethernet/IP, EtherCAT, OPC-UA, and IO-Link. They interface effortlessly with robots, HMIs, VFDs, servo amplifiers, and centralized SCADA systems, ensuring reliability and scalability.
Here are some of its most impactful features:
- High-Speed Processing Power
The core point of NX-ERA PLCs is that they are capable of real-time processing. These robot systems run as fast as your machinery, and the synchronization is important for the overall efficiency of the system. This compact PLC will guarantee flawless optimization for every aspect of the bottling line, be it controlling the work of conveyors or robotic manipulation.
- Modular Design for Flexibility
The greatest feature of the NX-ERA PLC is its modular design. Production plants in the automotive industry often aim for some form of adaptability, and, thus, this feature is very helpful. It allows the installation to expand while the business is developing. The implementation of modularity means that the system can be integrated with any new equipment, production units, or additional features to ensure that there will be no disruption to the system performance.
- Integrated I/O Modules for Streamlined Setup
Our smart and compact PLC integration contains integrated I/O modules that reduce installation and wiring times, thus also focusing on the fast-paced phenomenon in the automotive industry. For simplification of the things, input/output capabilities are now directly included in the integrated PLC system, which substantially reduces the external wiring as a result of which the setting up is speedier and less prone to mistakes.
- Advanced Web Server Capabilities
It is safe to say that we are far off the days when engineers would have to be on site for them to physically track and diagnose issues on the factory floor. The capability of the built-in web pages of our NX-ERA PLC allows easy remote access for getting the actual real-time state of the diagnostics and monitoring. This feature is incredibly important in an industry that operates around the clock, as it allows maintenance teams to resolve issues remotely, reducing downtime and keeping things running smoothly.
The Role of the NX-ERA PLCs in Material Handling
In the automotive industry, material handling is integral to the success of the production process. From raw materials to semi-finished goods, and finally to finished products, materials need to be handled with precision. Automation is key to achieving this, and Messung’s NX-ERA PLCs are designed to make this process as efficient and effective as possible.
Here is how it is done:
- Conveyor Systems Optimization
Conveyor systems, which carry parts between the workstations and at the same time keep the production continuously running, are the most popular form of material handling in the automotive plants. NX-ERA PLCs make sure that the system, no matter what, functions without any breaks by adjusting the speed of the conveyors to fit the pace of production. The real-time processing feature ensures that the system in question becomes flexible almost immediately, providing the assembly line without any interruptions and preventing the end line packing in the last round.
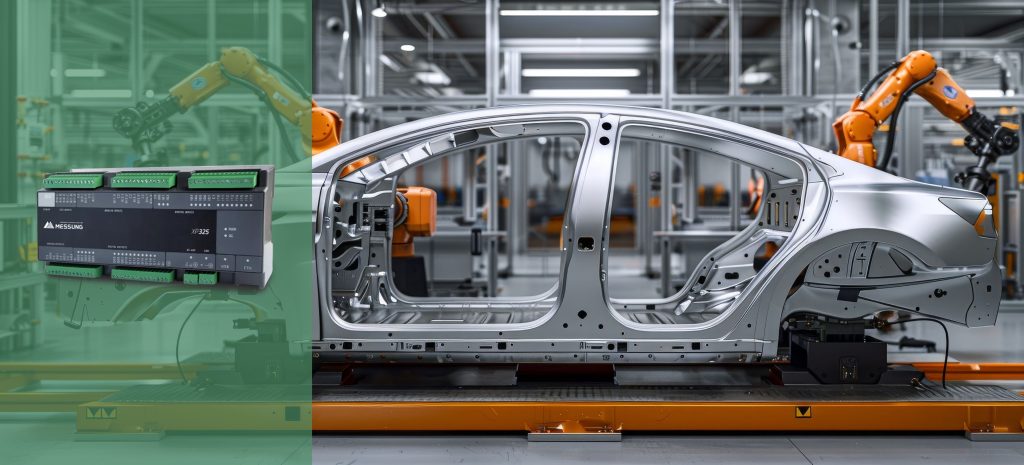
- Predictive Maintenance to Maximize Uptime
The predictive maintenance of the system is seen as the golden nugget to maximize uptime. For the maintenance of a plant, having machines down during their run time is quite expensive. In the automotive industry, where the production rates run on a very tight schedule, even a moment’s disruption would mean substantial losses. Our PLC Systems use a predictive maintenance system to keep a continuous check on the condition of the equipment. The control system will be equipped with predictive maintenance, which can track the system performance, increasing the change in predicting when maintenance is needed before failure occurs. These stains would reduce chances of equipment going down and also increase whole equipment machines productivity performance.
- Power Management for Material Handling Equipment
Automotive manufacturing plants consume vast amounts of electricity, particularly in material handling systems. From conveyor belts to cranes, these systems need reliable power sources. The NX-ERA PLC can be integrated into power solutions to ensure that energy is distributed efficiently. By preventing overloads, balancing loads, and monitoring consumption, the PLC helps reduce energy costs while ensuring that material handling equipment runs smoothly and without interruption.
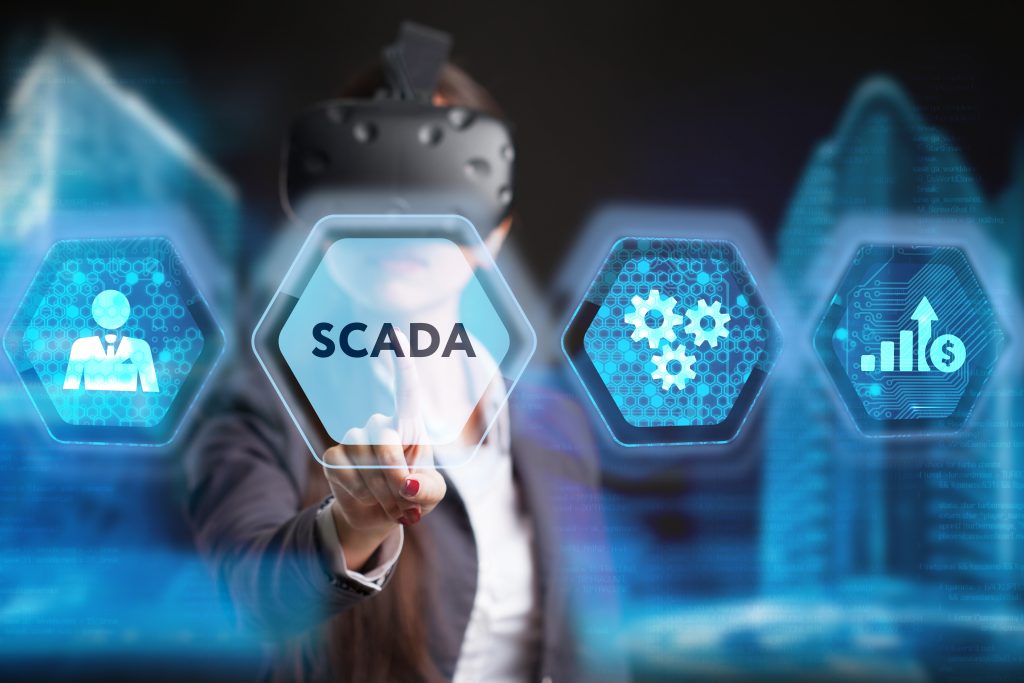
How NX-ERA PLCs Integrate with SCADA Systems
Industrial automation relies not just on PLCs but also on supervisory control and data acquisition (SCADA) systems to monitor and control large-scale operations. The integration of NX-ERA PLCs with SCADA applications enhances material handling capabilities by providing plant operators with real-time insights into the performance of material handling equipment.
- Real-Time Visualization and Data Monitoring
Data gathered from the cluster of service line sensors are then monitored by SCADA systems through real-time visualization and data troubling. By means of the material handling systems’ connecting to the SCADA applications, operators are able to visualize every operation stage on a single interface. Our NX-ERA PLC assists the SCADA system in a way that allows real-time data visualization. As for plant automation, this integration enables the operators to redesign the production line and fabricate the survey that they are in full command, including the conveyor speed, robotic movement, and electrical power consumption.
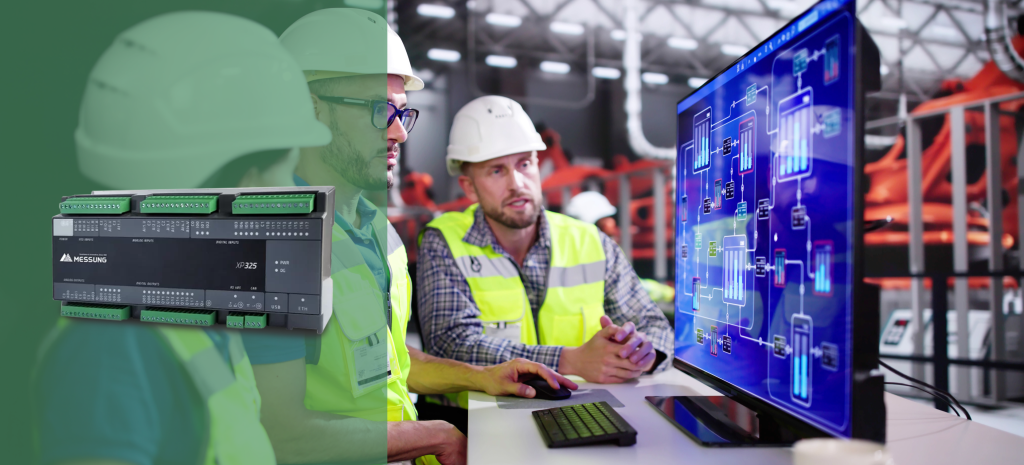
- Alarming and Fault Diagnostics
Unexpected malfunctions are a part of any complex system, but SCADA and PLC integration ensures they are dealt with swiftly. The NX-ERA PLC can send alerts to SCADA systems when material handling equipment encounters an issue, whether it’s a malfunction in a conveyor belt, a sensor failure in a robotic arm, or an electrical fault. This proactive approach helps resolve issues before they lead to extended downtime.
- Historical data analysis for continuous improvement
Other benefits of integrating the SCADA system with the NX-ERA PLC is to have an ability to analyse historical data. These past data performances can better help the plant managers to see trends, adjust production schedules, and improve the efficiency of the material-handling systems over the long period. In actuality, the PLC saves and disposes of necessary data. This information, then, is fed into the SCADA system and used for analysis and presentation purposes.
The Future of Material Handling with NX-ERA PLCs
As the automotive industry embraces Industry 4.0, NX-ERA PLCs are positioned at the forefront of the shift towards smarter, more connected manufacturing systems. This is brought about by switching to smarter, more connected production systems. Thanks to NX-ERA PLCs, which are able to integrate with SCADA applications, robots, and power supplies, you can now easily build a factory that can quickly adapt to changes in the current demand and the production process.
Benefits Include:
- More automation and efficiency with the increasing factories
As factories become more automated, the role of PLCs like the NX-ERA will only grow. The future of material handling will rely on even more precise and automated systems, from fully autonomous robots to smart conveyors that adjust their speed and behavior based on real-time conditions. The NX-ERA PLC is ready to support this evolution with its high-speed processing and robust integration capabilities.
- Energy Management and Sustainability
Green manufacturing is a critical concern for the industry today. Automotive manufacturers demand advanced NX-ERA PLCs in a bid to bring down the environmental impact of the production. An essential element that plays a pivotal role in power solutions, predictive maintenance, and derived data for operational efficiency is a way for these to reduce the consumption of energy.
- Real-Time Data and IoT Connectivity
With the rise of the Internet of Things (IoT) in manufacturing, NX-ERA PLCs will continue to integrate with a broader network of connected devices. This real-time data flow will empower automotive plants to make more informed decisions and improve their material handling systems.
Conclusion: The Future of Material Handling in the Automotive Industry
In the race for efficiency and innovation, Messung’s NX-ERA PLCs are the pit crew that keeps material handling equipment running at peak performance. Their combination of advanced features, modular design, and seamless integration with SCADA systems positions them as the ideal solution for automotive manufacturers aiming to stay ahead of the competition.
As automotive plants move towards smarter, more automated manufacturing processes, the need for reliable, high-performing PLCs like the NX-ERA will only continue to grow. By embracing the capabilities of Messung’s NX-ERA PLCs, automotive manufacturers can ensure that their material handling systems operate efficiently, sustainably, and with minimal downtime, ultimately contributing to the ongoing success of the industry.
In this fast-paced industry where precision is the name of the game, Messung’s NX-ERA PLCs are the game changers that automotive manufacturers need to optimize their material handling systems and maintain a competitive edge in the global market.